
Mould Making
Mould making involves coating the original sculpture with silicon rubber, prior to this if necessary the original is prepared – to ensure the best possible results. This may involve using a mould release agent or bracing a delicate original to ensure the form does not move with the weight of the mould materials to ensure the best possible results are achieved.

The sculpture shown has been scaled down from a 1.9m version using the latest scanning technology.

The rubber coating is applied to the entire surface of the original, and is able to pick up detail as fine as a finger print.

The rubber coating is constructed in sections to enable the mould to be removed from the original, and access to the inside surface of the mould for retrieval of the wax positive later on.
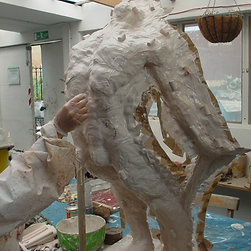
Keys are fixed to the surface of the setting rubber, to enable registration of the rubber to the caseing.


Resin and fibreglass casing is applied in sections over the surface of the rubber, which is then trimmed back and drilled to enable bolting together of the mould. As shown below


The case sections are then removed as part of the initial de-moulding stages, which continues with rubber sections being separated